Introduction
Manufacturing has a long history of applying quantitative methods for continual improvement. The most well-publicized case is Deming and how his methods revolutionized post-war Japan’s economy. Digital technological progress has profoundly expanded the data available to manufacturing operations that are already primarily data-driven. Manufacturers must use big data to exploit this development to improve efficiency and competitiveness fully. Big data is therefore necessary for manufacturers to enhance productivity and creativity; these technologies include cloud computing, IoT, and AI. This blog post explores how big data reshapes manufacturing through predictive maintenance, quality control, and supply chain optimization.
Section 1: Predictive Maintenance
Understanding Predictive Maintenance
Maintenance costs and downtime adversely affect manufacturers’ profitability and reputation. Therefore, preventative measures that reduce these problems from occurring are preferable. Furthermore, predictive maintenance involves identifying future issues and avoiding them. Moreover, several big data tools, including IoT sensors, data storage, data stream processing, and AI real-time analytics, support predictive maintenance. Firstly, IoT sensors support predictive maintenance by collecting real-time machine performance and health data. Big data storage allows sophisticated analytics tools to access high-volume, real-time IoT-generated data. AI analytics built on top of data stream processing frameworks analyze and identify patterns pointing to potential maintenance problems. Also, an added benefit is extending lifespan and optimizing resource allocation.
Key Technologies in Predictive Maintenance
Therefore, manufacturers that perform predictive maintenance will realize efficiencies and reliability. Predictive maintenance involves identifying problems that still need to be manifest. Thus, manufacturers need to analyze data on existing machine conditions to point out any potential issues that may arise. First, manufacturers must be able to collect data continually from machines and equipment. Manufacturers can gather continuous data from machines, particularly on performance and health, using Internet of Things sensors. Manufacturers, however, must manage this rapidly and massively created data utilizing big data in manufacturing. However, sophisticated data storage tools can manage storage and data access, often deployed on cloud platforms. These storage tools include NoSQL databases, HBase, and datalakes.
After that, engineers can create analytics tools on frameworks for streaming data, such as Apache Spark. Then, these analytics tools can forecast failure by detecting irregularities using machine learning models. These AI-driven analytics will, in turn, provide actionable insights for maintenance teams. Additional tools are data visualization tools that help maintenance teams track equipment health and performance.
For real-time data streaming, platforms like Apache Kafka are essential. Manufacturers can choose between managed services such as AWS Managed Streaming for Apache Kafka (MSK) and Confluent. Each offers distinct features and capabilities. For a detailed comparison to help determine the best fit for your predictive maintenance needs, refer to our in-depth analysis.
Benefits of Predictive Maintenance
Predictive maintenance has other critical benefits besides minimizing costly downtime and production interruptions. Associated with this benefit is that predictive maintenance enhances equipment reliability and improves operational efficiency. Also, because machinery requires regular maintenance, predictive maintenance can optimize these maintenance schedules and resource allocation. Another benefit is occupational health and safety by reducing incidents of unexpected machinery failures. These benefits, in turn, reduce maintenance costs and improve return on investment.
Challenges in Implementing Predictive Maintenance
Organizations planning to implement predictive maintenance within their operations must consider several challenges. One challenge is that their existing machinery often needs more design to interface with IoT devices. Therefore, this challenge complicates the integration of IoT devices with existing machinery. The next challenge is that these IoT devices generate vast data sets taxing IT resources. Therefore, organizations must invest in IT infrastructure or utilize cloud computing. These and other factors contribute to high initial costs for implementing predictive maintenance systems. Due to interconnection, integrating machinery with other data systems generates data security and privacy concerns. Finally, organizations must ensure machine data accuracy and reliability for accurate predictions that guarantee effective predictive maintenance.
Future Trends in Predictive Maintenance
Several trends will further transform predictive maintenance’s impact on manufacturing. Vendors are building their platforms to have enhanced data interoperability and standardization with other platforms. They are also developing more sophisticated IoT sensors and devices to complement these platforms. In addition, predictive analysis further embraces the increased adoption of AI and machine learning. Augmented reality integration is an exciting field for maintenance training and support. Increasing interoperability between these platforms will further increase cybersecurity’s role.

Section 2: Quality Control
Enhancing Quality Control with Big Data
Manufacturers who fail to manage production quality effectively will inevitably fail. Big Data in Manufacturing drives data-driven quality control, helping manufacturers better manage production quality. The first step is gathering accurate data on production processes and product attributes. The next is performing real-time analytics on this data to detect defects and deviations from quality standards. Subsequently, these data-driven insights enable rapid response to quality issues. This allows manufacturers to ensure consistent product quality and customer satisfaction.
Key Technologies in Quality Control
Several technologies enable data-driven quality control, including IoT devices, stream processing frameworks, cloud platforms, AI-driven analytics, and data visualization. IoT devices gather production parameters and detect anomalies. Previously, manufacturers only sampled products for quality control because checking all products was too expensive. Stream processing frameworks like Spark allow manufacturers to build analytics tools for continuous real-time product data. In turn, cloud platforms facilitate data sharing and collaboration across teams. Machine learning applied to product data helps to identify patterns indicative of defects. At the same time, AI-driven analytics provide predictive insights into quality trends. Finally, data visualization tools assist operators in tracking quality metrics and performance.
Benefits of Data-Driven Quality Control
Data-driven quality control enables manufacturers to manage product quality better in several key areas. It primarily reduces defects and rework, thereby reducing costs. Next, it improves customer satisfaction through consistent product quality, lowering replacements, remediation, and recalls. Another area involves improving compliance with industry standards and regulations. Data-driven quality control also enables faster identification and quality issue resolution. These all contribute to proactive quality management and continuous improvement.
Challenges in Implementing Quality Control
Manufacturers implementing data-driven quality control need to consider specific considerations. Data-driven quality control entails interconnected data systems, and manufacturers must address data privacy and cybersecurity concerns. Quality control based on generated manufacturing data depends upon the data’s accuracy and reliability. Next, while data-driven quality control reduces quality costs, there remains a balance between quality improvements and production efficiency. Also, data-driven quality entails collecting data from diverse sources, and integrating this data is challenging. The generated data sets are large and complex, and operators need advanced analytical skills.
Future Trends in Quality Control
Several trends promise to improve data-driven quality impact on the manufacturing process. Greater use of AI and machine learning will further enhance quality prediction. Manufacturers are never an island and depend on supplier quality. Therefore, integrating blockchain will allow traceability and transparency between dependent organizations. IoT sensors will continue to advance and improve real-time monitoring. Digital twins of manufacturing processes will lead to more realistic simulation and superior quality process optimization. Industries as a whole will place greater emphasis on data-driven quality management. Therefore, manufacturers will need to address this.
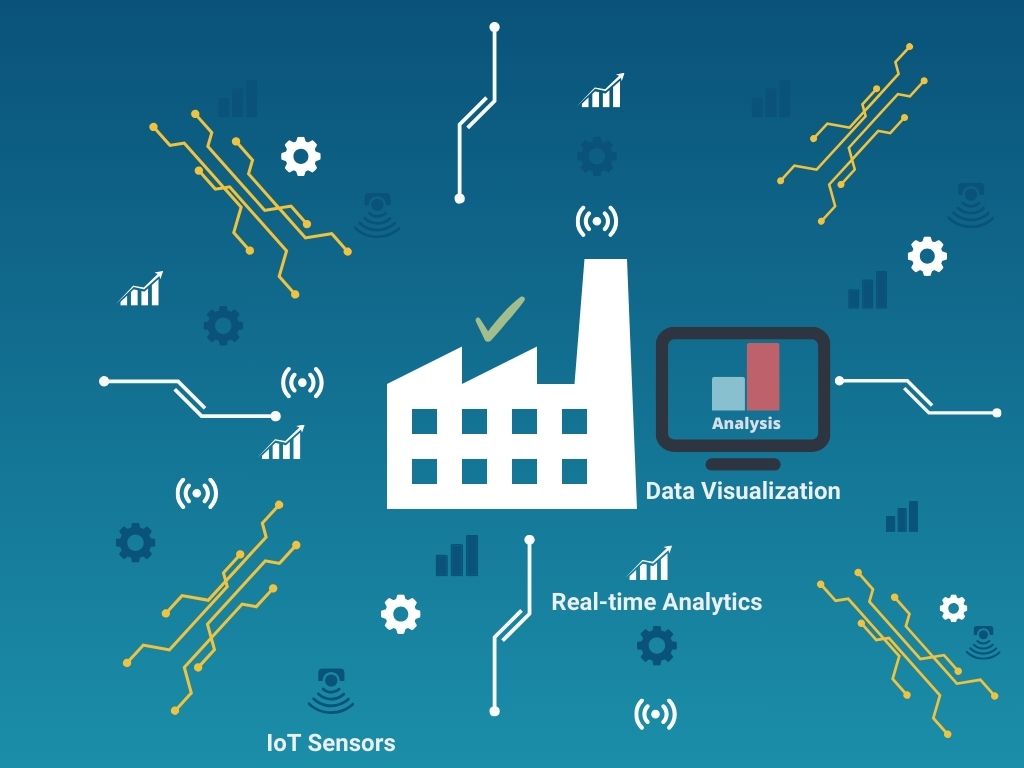
Section 3: Supply Chain Optimization
The Role of Big Data in Supply Chain Optimization
No manufacturer is an island but must operate in an ecosystem of upstream and downstream organizations. These organizations include raw material suppliers, component manufacturers, assembly manufacturers, and wholesale and retail outlets. Data-driven supply chain management improves participant collaboration, cooperation, and performance. Participants can track shipments and monitor supply chain conditions in real time. Analytics on real-time data also enhances supply chain efficiency and agility. Insights from real-time data enable participants to perform superior demand forecasting and inventory management. Participants can also apply AI algorithms to optimize logistics and reduce supply chain disruptions.
Key Technologies in Supply Chain Optimization
Participants in a supply chain generate vast and diverse data at high velocity. Therefore, it is necessary to utilize big data in manufacturing to manage, integrate, and process all this data. IoT sensors facilitate automated data collection, allowing real-time visibility into supply chain activities. Big data storage technologies, including NoSQL databases on cloud platforms, facilitate data integration and collaboration across supply chain partners. Data lakes also contribute to integrating diverse data types. Blockchain technology with zero trust builds confidence in data validity by all participants. Next, machine learning models utilize this data to predict demand patterns for inventory optimization. Participants can also apply AI-driven analytics to identify inefficiencies and recommend improvements. Finally, data visualization tools assist operators in monitoring supply chain performance metrics.
Benefits of Data-Driven Supply Chain Optimization
Making supply chain ecosystems data-driven has several key benefits. First, it enhances supply chain transparency, traceability, and accountability, strengthening participant relationships and collaboration. Equally important is that it increases supply chain resilience and responsiveness to disruptions. Alongside these benefits, data-driven supply chains provide the opportunity for cost savings by optimizing logistics and transportation. It also contributes to inventory cost management by improving demand forecasting.
Challenges in Implementing Supply Chain Optimization
Several vital considerations arise when supply chain participants share data. The primary concern is data security and privacy whenever one participant shares data with others. Participants need to build an enforceable data governance framework to address these concerns. Associated with this is data quality regarding accuracy and timeliness on which decisions are based. Blockchain technologies can assist with accountability and enforcement. Implementation challenges include the complexity of data integration from multiple sources. Global supply chain management is highly complex, and requirement processes besides big data. There are also sustainability and ethical considerations impacting any potential cost savings.
Future Trends in Supply Chain Optimization
Several trends promise to transform supply chains and further cooperation between participants. The most critical trend is cybersecurity’s growing importance in these networks and the development of hardened data governance frameworks. The next significant trend is blockchain evolution and integration into supply chains for transparency and accountability. Another significant development is the rapid progress in AI and machine learning for improved supply chain analytics. These developments will lead to autonomous supply chain development along with robotics. Finally, increasing data-driven supply chain strategies will lead to a greater emphasis on sustainability and ethical sourcing.

Section 4: Cost Reduction
Leveraging Big Data for Cost Reduction
This article has touched upon cost management and cost reduction earlier. It has demonstrated that data-driven manufacturing supports more informed decision-making and strategies around cost management. Improving resource allocation and reducing waste enables us to achieve this. IoT sensors collect data to monitor resource consumption and optimize energy usage. Manufacturers can apply analytics to this data to identify cost-saving opportunities. They can further analyze production processes for efficiency improvements.
Key Technologies in Cost Reduction
This article has covered many key technologies but will discuss them here, emphasizing cost reduction. IoT sensors gather factory data and perform intelligence on that data to track resource consumption and identify inefficiencies. Because this data is vast and diverse, manufacturers need big data in manufacturing technologies, including storage and ready access. Cloud platforms complement big data storage by facilitating data sharing and collaboration for cost analysis. Manufacturers can then apply machine learning models to this data to optimize production schedules and resource allocation. Additionally, AI-driven analytics provide insights into cost drivers and reduction opportunities, making cost management more data-driven. Finally, data visualization tools assist operators in viewing this data, allowing them to monitor cost performance and trends.
Benefits of Data-Driven Cost Reduction
All organizations have cost management as a core strategy, and manufacturers are no exception. Organizations aim to improve profitability by expanding sales and reducing costs. A data-driven approach to manufacturing manages costs through improved resource allocation and waste minimization. It also supports continuous improvement and innovation in cost reduction. This, in turn, enables better budget planning and cost management. By making production more cost-efficient, manufacturers can enhance competitiveness.
Challenges in Implementing Cost Reduction
Making cost reduction more data-driven introduces challenges that manufacturers need to address. Manufacturers must address data privacy and cybersecurity concerns associated with data methods and processes. Organizations must address data accuracy and reliability associated with data methods for effective cost analysis. Manufacturers must balance cost reduction with quality and innovation objectives, a classic project management trade-off. Even though making cost reduction data-driven, it remains complex when identifying and prioritizing cost reduction opportunities. Finally, many cost-reduction initiatives impact the workforce and operations. Management needs to navigate these issues wisely.
Future Trends in Cost Reduction
The following trends will further transform cost reduction in manufacturing. Continual progress in IoT integration and automation will continue to improve resource efficiency. Also, progress in developing more sophisticated data analytics tools for improved cost analysis. AI and machine learning will complement these analysis tools for further cost optimization. These trends will combine to make data-driven decision-making more prominent in cost management. Increasing emphasis on sustainable cost-reduction strategies will become essential in manufacturing processes.
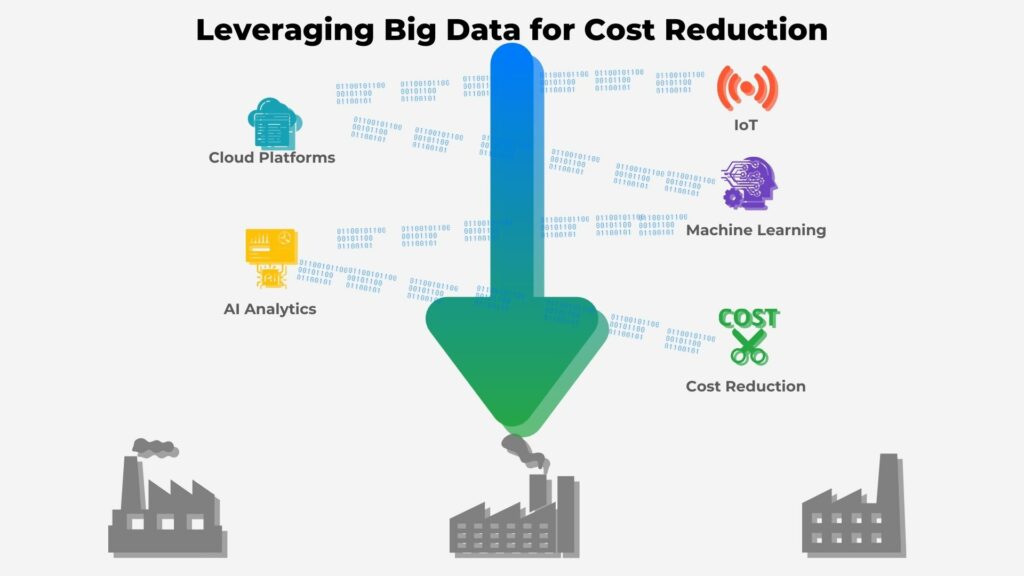
Section 5: Innovation and Product Development
Driving Innovation with Big Data
Product development and innovation are essential dimensions of any manufacturer’s competitiveness. Manufacturers must also collect customer feedback and usage data to make product improvement more data-driven. They also need to obtain data-driven insights into market trends and consumer preferences. These data-driven insights will support rapid prototyping and iterative product development. Furthermore, data-driven insights allow manufacturers to create personalized products for individual consumers.
Key Technologies in Innovation and Product Development
As mentioned earlier, big data technologies in manufacturing also support innovation and product development. IoT sensors embedded in products gather real-time data on product performance and usage. Cloud platforms hosting big data storage technologies support the management of vast and diverse data collected from products in real-time. They also support the management of consumer and market data and facilitate collaboration and data sharing for innovation. Manufacturers apply both machine learning models and AI-driven analytics to this data. Machine learning models identify emerging trends and consumer needs, whereas AI-driven analytics provide insights into market opportunities and risks. Finally, data visualization tools assist product developers in tracking innovation metrics and performance.
Benefits of Data-Driven Innovation
Data-driven innovation enables agile and iterative innovation by providing near real-time feedback on product innovations. This, in turn, accelerates product development and time to market while enhancing product quality and customer satisfaction. Data-driven product development also enables personalization and product customization. These benefits combine to strengthen competitive advantage through innovative and customized offerings.
Challenges in Implementing Data-Driven Innovation
Data-driven product innovations have several challenges. The key challenges are cybersecurity and data privacy concerns. The concerns highlight data privacy since manufacturers obtain consumer usage data, which is highly sensitive for many product types. Data-driven product development is only effective when its data is accurate and reliable. Integrating this data is also complex due to its derivation from diverse sources. Also, manufacturers must balance innovation activities with cost and resource constraints. Finally, manufacturers must also navigate the cultural shift towards data-driven innovation.
Future Trends in Innovation and Product Development
Several unique trends have the potential to disrupt product development further. Synthesizing IoT and AR/VR technologies will provide immersive product experiences, allowing manufacturers to prototype new product innovations rapidly. This will support virtual prototyping and testing, making product development more agile and iterative. Data-driven approaches will improve collaboration and co-creation and allow developers to apply AI and machine learning for personalized products. Finally, there is a growing movement around sustainable and ethical innovation in manufacturing.

Conclusion
Big data is making manufacturing more data-driven, driving innovation and enhancing efficiency. Data-driven operations and decision-making make manufacturers more competitive in the evolving landscape and impact several key areas in manufacturing. These include predictive maintenance, quality control, supply chain optimization, cost reduction, and product innovation. However, there are several challenges to increasing the dependence upon data and data-driven operations, with cybersecurity being the most critical. Other challenges include data validity, volume, and integration from diverse sources. Manufacturers must embrace big data technologies to thrive in the era of Manufacturing 4.0.